Fixing radiators to internal walls
A number of different types of internal wall will be found; masonry plaster, stud wall (either plasterboard or lathe and plaster), plasterboard dry lining. Which type of wall you have, will affect how you fix the radiator brackets but first of all you need to decide upon the position of the radiator and its brackets.
Positioning the radiator
Radiators are normally fitted central to a feature; a window, alcove or wall - where a door opens back onto a wall, radiators are normally positioned central on the exposed wall with the door open. None of this is critical and can be ignored if a more appropriate position is decided upon.
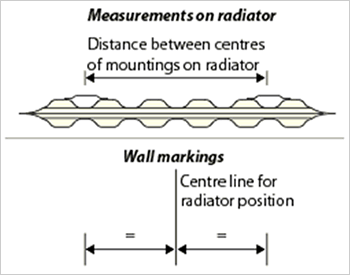
The first thing to do is to mark on the wall the vertical centre line for the radiator. Then, on the back of the radiator, measure the distance between the middle of the supports mountings, divide this distance by 2 to establish the offset required on both sides of the line marked on the wall.
For the vertical position of the radiator, it's normal for the bottom of the radiator to be 4 to 6 inches above the floor - try to use the same height as used for any existing radiators.
On the back of the radiator, measure up from the bottom to the lower edge of the support bracket. This distance plus the required distance from the floor is the required height from the floor for the lower support on the wall bracket.
Note that most radiator wall brackets have faces of unequal depth, both machined to support the radiator - it does not matter which support face is used but the deeper one may be necessary for the pipes to the radiator to clear any skirting board.
The method of fixing the brackets to the wall depends upon the type of wall construction - see below for masonry plaster, stud walling, or plasterboard dry lining walls.
Masonry plaster walls:
Strong fixings can be easily made on most masonry walls just by using screws and wall plugs.
Place each bracket on the wall in turn, line up the mounting face with the vertical lines marked on the wall and the height of the lower support the required distance from the floor. The bracket towards the end of the radiator with the bleed valve should be slightly higher than the other to allow any air to escape through the valve. Mark the fixing points - where the brackets have slots and holes, use a hole at the top and a slot lower down.
Drill and plug the wall then screw the brackets in place. Make sure you have good solid fixings and remember to check for pipes, cables etc in the wall before drilling.
If one of the top holes hits a mortar joint between the bricks/blocks, this may be a weak point especially where lime mortar has been used - it is best to reposition such a hole into a brick/block by using one of the alternative mounting holes/slots in the bracket making sure that the vertical height of the bracket remains as required.
Some clay bricks (mainly old ones) and true concrete blocks contain hard pieces (flints etc) which can cause a drill bit to run off line - this shouldn't cause a problem as the radiator supports on the back of radiators are normally 50mm or so wide so any small sidewise misalignment can easily be accommodated.
Some blocks (such as modern high insulation types) are extremely soft, always drill these carefully to avoid over-enlarging the hole and use the special wall plugs.
Stud walling (both lathe and plaster and plasterboard):
Do not fix radiators just to the plasterboard (or lathe and plaster), sufficient support can only be achieved when fixings the brackets either to the vertical timbers (the studs) or using battens fixed to the uprights across the front face of the wall.
Studs are normally set at equal distances apart - on older stud walls they are usually no greater than 405mm (16 inches) apart, while in more modern stud walls, the maximum spacing is about 600mm (24 inches).
To find the position of the studs behind plasterboard, lightly knock on the wall while moving sideways - the studs should sound solid while the spaces between should sound hollow. It is not so easy to locate the studs holding up lathe and plaster finishes as there is no discernible difference in the sound of a knock.
When all else fails, the last resort is to draw a horizontal line where the fixing is required and to drill small holes along the line about 25mm (1 inch) apart until solid timber (i.e. a stud) is located. Once the first stud has been located, measure along the line in multiples of 405mm (16 inches) and drill through to confirm the location of the next stud - if further studs cannot be located in this way, the only option is to drill another series of small holes until a stud is found.
It is possible (though unlikely) that two studs will coincide with the horizontal spacing required for the radiator brackets, in this case:
- Offer up each bracket in turn on the appropriate studs at the required height and mark through the fixing holes in the brackets.
- Carefully drill clearance holes through the plasterboard (or lathe and plaster).
- Secure the brackets to the vertical studs. Lathe and plaster walls may crack when the brackets are tightened down onto the surface as the lathes are compressed.
Where the studs do not coincide with the spacing:
- Offer up each bracket in turn on the wall and mark the height of the fixing holes in the brackets.
- Make 2 timber horizontal battens - make the battens long enough so that they can be fixed to the studs beyond the positions for the mounting brackets. Mark and drill clearance holes in each batten to coincide with each vertical stud along its length.
- Align the centre of each batten with the height marks for the bracket fixing holes, mark through the batten.
- Carefully drill clearance holes through the plasterboard (or lathe and plaster). Secure the battens to the vertical studs using screws. Lathe and plaster walls may crack when the battens are tightened down onto the surface as the lathes are compressed.
- Position and secure the brackets to the horizontal battens at the appropriate height.
Dry Lining walls:
Dry lining is possibly the most difficult type of wall to hang a radiator on as the surface plasterboard is only supported by 'blobs' of adhesive, the plasterboard alone will not provide adequate support and any attempt to pull down the brackets onto the unsupported surface will cause the plasterboard to deform.
A practical solution is to:
- Identify on the wall where the fixings will go.
- Offer up each bracket in turn and mark around it, then cut out the plasterboard about 5mm within the marked profile.
- Make timber spacers which will fill the gap between the blockwork behind the plasterboard and the front surface of the plasterboard. The cut-outs and spacers, being smaller than the brackets, will be hidden by the brackets.
- Drill clearance holes in the timber spacers to correspond with the position of the bracket fixings.
- Fix the brackets to the wall using screws through the spacers into plugs in the blockwork.
|